Taladro de banco
Es una máquina herramienta donde se mecanizan la mayoría de los agujeros que se hacen a las piezas en los talleres mecánicos. Destacan estas máquinas por la sencillez de su manejo. Tienen dos movimientos: El de rotación de la broca que le imprime el motor eléctrico de la máquina a través de una transmisión por poleas y engranajes, y el de avance de penetración de la broca, que puede realizarse de forma manual sensitiva o de forma automática, si incorpora transmisión para hacerlo.
Se llama taladrar a la operación de mecanizado que tiene por objeto producir agujeros cilíndricos en una pieza cualquiera, utilizando como herramienta una broca. De todos los procesos de mecanizado, el taladrado es considerado como uno de los procesos más importantes debido a su amplio uso y facilidad de realización, puesto que es una de las operaciones de mecanizado más sencillas de realizar y que se hace necesario en la mayoría de componentes que se fabrican.
Producción de agujeros
Los factores principales que caracterizan un agujero desde el punto de vista de su mecanizado son:
-
Diámetro
-
Calidad superficial y tolerancia
-
Material de la pieza
-
Material de la broca
-
Longitud del agujero
-
Condiciones tecnológicas del mecanizado
-
Cantidad de agujeros a producir
-
Sistema de fijación de la pieza en el taladro.
Hay dos tipos de agujeros diferentes los que son pasantes y atraviesan en su totalidad la pieza y los que son ciegos y solo se introducen una longitud determinada en la pieza sin llegarla a traspasar, tanto unos como otros pueden ser lisos o pueden ser roscados.
Respecto de los agujeros pasantes que sirven para incrustar tornillos en ellos los hay de entrada avellanada, para tornillos de cabeza plana, agujeros de dos diámetros para insertar tornillos allen y agujeros cilíndricos de un solo diámetro con la cara superior refrentada para mejorar el asiento de la arandela y cabeza del tornillo. El diámetro de estos agujeros corresponde con el diámetro exterior que tenga el tornillo.
Respecto de los agujeros roscados el diámetro de la broca del agujero debe ser la que corresponda de acuerdo con el tipo de rosca que se utilice y el diámetro nominal del tornillo. En los tornillos ciegos se debe profundizar más la broca que la longitud de la rosca por problema de la viruta del macho de roscar.


Torno
Conjunto de máquinas y herramientas que permiten mecanizar, cortar, fisurar, trapeciar, y ranurar piezas de forma geométrica por revolución. Estas máquinas-herramienta operan haciendo girar la pieza a mecanizar (sujeta en el cabezal o fijada entre los puntos de centraje) mientras una o varias herramientas de corte son empujadas en un movimiento regulado de avance contra la superficie de la pieza, cortando la viruta de acuerdo con las condiciones tecnológicas de mecanizado adecuadas.
La herramienta de corte va montada sobre un carro que se desplaza sobre unas guías o rieles paralelos al eje de giro de la pieza que se tornea, llamado eje X; sobre este carro hay otro que se mueve según el eje Y, en dirección radial a la pieza que se tornea, y puede haber un tercer carro llamado charriot que se puede inclinar, para hacer conos, y donde se apoya la torreta portaherramientas. Cuando el carro principal desplaza la herramienta a lo largo del eje de rotación, produce el cilindrado de la pieza, y cuando el carro transversal se desplaza de forma perpendicular al eje de simetría de la pieza se realiza la operación denominada refrentado.
Los tornos copiadores, automáticos y de control numérico llevan sistemas que permiten trabajar a los dos carros de forma simultánea, consiguiendo cilindrados cónicos y esféricos. Los tornos paralelos llevan montado un tercer carro, de accionamiento manual y giratorio, llamado charriot, montado sobre el carro transversal. Con el charriot inclinado a los grados necesarios es posible mecanizar conos. Encima del charriot va fijada la torreta portaherramientas.
Torno paralelo
El torno paralelo o mecánico es el tipo de torno que evolucionó partiendo de los tornos antiguos cuando se le fueron incorporando nuevos equipamientos que lograron convertirlo en una de las máquinas herramientas más importante que han existido. Sin embargo, en la actualidad este tipo de torno está quedando relegado a realizar tareas poco importantes, a utilizarse en los talleres de aprendices y en los talleres de mantenimiento para realizar trabajos puntuales o especiales.
Para la fabricación en serie y de precisión han sido sustituidos por tornos copiadores, revólver, automáticos y de CNC. Para manejar bien estos tornos se requiere la pericia de profesionales muy bien calificados, ya que el manejo manual de sus carros puede ocasionar errores a menudo en la geometría de las piezas torneadas.


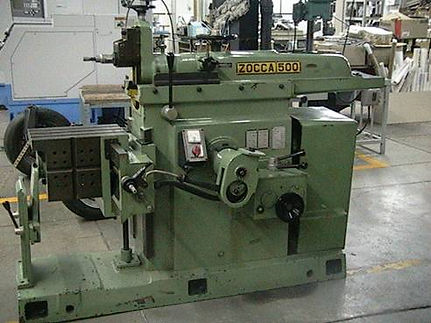


Cepillo de codo
El cepillo de codo es una máquina para dar acabado a piezas ya empezadas en el torno. Existen unas piezas llamadas piezas caprichosas que son las piezas que sólo se pueden hacer en máquinas como la fresadora o el cepillo de codo.
Partes
-
Carnero o Ariete
-
Fraile
-
Opresor
-
Manivela del carro vertical
-
La viela
-
Motor eléctrico
-
Palanca del Ariete
-
La transmisión
-
Piñón
-
Bandas
-
Poleas
-
Mesa transversal y Graduada
-
Bancada de la mesa
-
Estructura
-
Corona
-
Cabezal
Fresadora
Una fresadora es una máquina herramienta utilizada para realizar trabajos mecanizados por arranque de viruta mediante el movimiento de una herramienta rotativa de varios filos de corte denominada fresa.
Mediante el fresado es posible mecanizar los más diversos materiales, como madera, acero, fundición de hierro, metales no férricos y materiales sintéticos, superficies planas o curvas, de entalladura, de ranuras, de dentado, etc. Además las piezas fresadas pueden ser desbastadas o afinadas. En las fresadoras tradicionales, la pieza se desplaza acercando las zonas a mecanizar a la herramienta, permitiendo obtener formas diversas, desde superficies planas a otras más complejas.
Debido a la variedad de mecanizados que se pueden realizar en las fresadoras actuales, al amplio número de máquinas diferentes entre sí, tanto en su potencia como en sus características técnicas, a la diversidad de accesorios utilizados y a la necesidad de cumplir especificaciones de calidad rigurosas, la utilización de fresadoras requiere de personal cualificado profesionalmente, ya sea programador, preparador o fresador.
El empleo de estas máquinas, con elementos móviles y cortantes, así como líquidos tóxicos para la refrigeración y lubricación del corte, requiere unas condiciones de trabajo que preserven la seguridad y salud de los trabajadores y eviten daños a las máquinas, a las instalaciones y a los productos finales o semielaborados.
Las herramientas de corte más utilizadas en una fresadora se denominan fresas, aunque también pueden utilizarse otras herramientas para realizar operaciones diferentes al fresado, como brocas para taladrar o escariadores. Las fresas son herramientas de corte de forma, material y dimensiones muy variados de acuerdo con el tipo de fresado que se quiera realizar. Una fresa está determinada por su diámetro, su forma, material constituyente, número de labios o dientes que tenga y el sistema de sujeción a la máquina.
Rectificadora
La rectificadora es una máquina herramienta, utilizada para realizar mecanizados por abrasión, con mayor precisión dimensional y menores rugosidades que en el mecanizado por arranque de viruta.
Las piezas que se rectifican son principalmente de acero endurecido mediante tratamiento térmico. Para el rectificado se utilizan discos abrasivos robustos, llamados muelas. El rectificado se aplica luego que la pieza ha sido sometida a otras máquinas herramientas que han quitado las impurezas mayores, dejando solamente un pequeño excedente de material para ser eliminado por la rectificadora con precisión. A veces a una operación de rectificado le siguen otras de pulido y lapeado, como por ejemplo en la fabricación de cristales para lentes.
Las rectificadoras para piezas metálicas consisten en un bastidor que contiene una muela giratoria compuesta de granos abrasivos muy duros y resistentes al desgaste y a la rotura. La velocidad de giro de las muelas puede llegar a 30.000 rpm, dependiendo del diámetro de la muela.
Según las características de las piezas a rectificar se utilizan diversos tipos de rectificadoras, siendo las más destacadas las siguientes:
-
Las rectificadoras planeadoras o tangenciales consisten de un cabezal provisto de una muela y un carro longitudinal que se mueve en forma de vaivén en el que se coloca la pieza a rectificar. También puede colocarse sobre una plataforma magnética. Generalmente se utiliza para rectificar matrices, calzos y ajustes con superficies planas.
-
La rectificadora sin centros (centerless) consta de dos muelas y se utilizan para el rectificado de pequeñas piezas cilíndricas, como bulones, casquillos, pasadores, etc. Permite automatizar la alimentación de las piezas, facilitando el funcionamiento continuo y la producción de grandes series de la misma pieza. En este caso la superficie de la pieza se apoya sobre la platina de soporte entre el disco rectificador (que gira rápidamente) y la platina regulable pequeña (que se mueve lentamente).
-
Las rectificadoras universales se utilizan para todo tipo de rectificados en diámetros exteriores de ejes. Son máquinas de gran envergadura cuyo cabezal portamuelas tiene un variador de velocidad para adecuarlo a las características de la muela que lleva incorporada y al tipo de pieza que rectifica.

CNC
El control numérico o control decimal numérico (CN) es un sistema de automatización de máquinas herramienta que son operadas mediante comandos programados en un medio de almacenamiento, en comparación con el mando manual mediante volantes o palancas.
Las primeras máquinas de control remoto numéricos se construyeron en los años 40 y 50, basadas en las máquinas existentes con motores desmodificados cuyos números se relacionan manualmente siguiendo las instrucciones dadas en un microscopio de tarjeta perforada. Estos servomecanismos iniciales se desarrollaron rápidamente con los equipos analógicos y digitales. El abaratamiento y miniaturización de los procesadores ha generalizado la electrónica digital en los toros herramienta, lo que dio lugar a la denominación control decimal numérico, control numérico por computadora , control numérico por computador o control numérico computarizado (CNC), para diferenciarlas de las máquinas que no tenían computadora. En la actualidad se usa el término control numérico para referirse a este tipo de sistemas, con o sin computadora.1
Este sistema ha revolucionado la industria debido al abaratamiento de microprocesadores y a la simplificación de la programación de las máquinas de CNC.
El sistema se basa en el control de los movimientos de la herramienta de trabajo con relación a los ejes de coordenadas de la máquina, usando un programa informático ejecutado por un ordenador.
En el caso de un torno, hace falta controlar los movimientos de la herramienta en dos ejes de coordenadas: el eje de las X para los desplazamientos longitudinales del carro y el eje de las Z para los desplazamientos transversales de la torre.
En el caso de las fresadoras se controlan también los desplazamientos verticales, que corresponden al eje Y. Para ello se incorporan servomotores en los mecanismos de desplazamiento del carro y la torreta, en el caso de los tornos, y en la mesa en el caso de la fresadora; dependiendo de la capacidad de la máquina, esto puede no ser limitado únicamente a tres ejes.

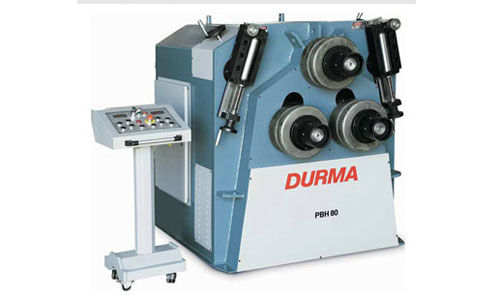
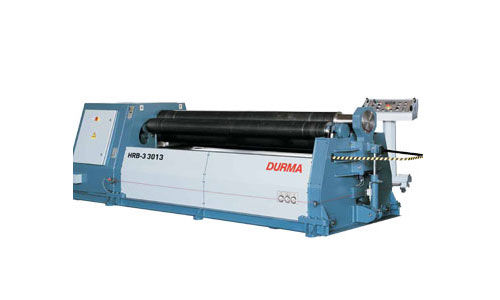

Dobladora de tubos
Una máquina dobladora de tubos utiliza un cilindro hidráulico para doblar tubos de acero de grosor considerable.
La fuerza necesaria para doblar los tubos es de40.000N en los 500 mm en los que el cilindro desplaza la matriz curva.
El proceso de doblado debe durar 12 segundos para conseguir un rendimiento óptimo respecto a las propiedades del tubo doblado y la productividad de la máquina.
Cuando tenga que doblar un trozo de tubo blando y no tiene a la mano una herramienta correspondiente, puede usted improvisar una dobladora muy eficiente con una polea de banda V. Escoja una polea con el diámetro que pueda proporcionarle la curva deseada. Luego deslice una varilla por el agujero del eje y usela para sostener la polea en posición vertical contra el piso mediante su pie, mientras dobla el tubo en su derredor.
Aplique una presión lenta y uniforme y producirá usted una curva perfecta en el tubo, sin aplastarlo en lo más mínimo.
¿Cómo se dobla un tubo? Cuando un tubo se dobla, la pared que forma la parte externa del doblez se elonga y adelgaza mientras que la pared que forma la parte interna del tubo se comprime y engrosa .Un objetivo común al doblar un tubo es formar un doblez uniforme. Esto es sencillo de lograr cuando el tubo tiene un grosor de pared ancho y se dobla en un radio amplio .Para determinar el grosor de un tubo se compara su diámetro interno y su diámetro externo. El resultado de dividir el diámetro externo y el interno nos da el factor de pared del tubo.
Punteadora
Las punteadoras mecánicas son máquinas soldadoras de brazo móvil operadas por pedal. La estructura del chasis de estas punteadoras mecánicas está probada para muchos años de servicio proporcionando puntos de soldadura de alta calidad. Contamos con tres tamaños de chasis con distintos transformadores, garantizando así una máquina adecuada para cualquier espesor de lámina.
-
Punteadoras Mecánicas Tamaño 1 - 5, 7 y 10 KVA
-
Punteadoras Mecánicas Tamaño 2 - 15, 20 y 30 KVA
-
Punteadoras Mecánicas Tamaño 3 - 50 y 75 KVA
Presión de las Punteadoras Mecánicas: La presión adecuada entre los electrodos es uno de los requerimientos básicos para lograr un punto de calidad. Las máquinas operadas mecánicamente están limitadas con la presión máxima alcanzable y ésta disminuya con gargantas largas.
La operación en punteadora neumática asegura la presión adecuada en cualquier garganta. Las máquinas neumáticas también garantizan el aprovechamiento máximo del equipo y menos fatiga del operario. Ver Punteadoras Neumáticas.
Transformadores de alto rendimiento enfriados por agua. la corriente de soldadura y su suministro es un factor decisivo en el diseño de una máquina punteadora, el transformador SPOT WELDING es de núcleo acorazado con sus primarios y secundarios en forma de "sandwich", los secundarios están enfriados y su construcción proporciona alta eficiencia y larga vida. Todos los aislamientos del transformador son Clase H. Todos los transformadores tienen un conmutador de siete posiciones de calor y "OFF".
Controles. Es muy importante que su máquina punteadora tenga un control de flujo de corriente de soldadura, para asegurar que en producción, todas las piezas punteadas salgan iguales, todos los controles están construidos en estado sólido con circuitos impresos y componentes enchufados.
Roladora de perfiles
Máquina curvadora universal para perfiles, capaz de curvar cualquier tipo de perfil de acero, aluminio, acero inoxidable y otras aleaciones.
Máquina con tres rodillos, uno superior y dos inferiores, todos ellos con tracción motorizada electromecánica y superficie lisa, lo que permite obtener un curvado óptimo con cualquier perfil sin dañar su superficie igual que permite obtener diámetros muy cerrados sin problemas.
Los dos rodillos inferiores tienen movimiento independiente uno del otro lo que permite el precurvado y ajustes finos para cerrar los diámetros; el rodillo superior es fijo. En este modelos el ascenso y descenso de los rodillos inferiores es en forma hidráulica mediante pistones y la lectura de su posición es mediante visualizadores mecánicos.
La máquina está equipada con un juego de rodillos que combinados entre si nos permiten curvar cualquier perfil que contenga un plano. Para el caso del tubo se requieren rodillos especiales para cada diámetro de tubo que se pretenda curvar.
Los rodillos dobladores de placa u hoja se ofrecen en dos diferentes categorías: apriete sencillo y apriete doble, pero pueden variar en geometría o estilo. Los estilos de máquina generales son sistemas con apriete inicial de tres rodillos, apriete doble de tres rodillos, apriete doble de cuatro rodillos, traslación va-riable de tres rodillos, pirámide de tres rodillos, y sistemas de dos rodillos. Los rodillos de placa también se construyen en un formato vertical para aplicaciones especiales. Es importante combinar el estilo de máquina más apropiado con la aplicación.
Roladora de lámina
Una máquina roladora de láminas es una herramienta que permite el enrollado de una hoja de metal. Ésta adopta una tecnología de laminación única y provee alta precisión en el pre-plegado. La interfaz digital Hombre-máquina hace de ésta una operación sencilla, confiable y eficiente.
La máquina roladora de láminas permite dar al material diferentes formas. Se caracteriza por su estructura compacta y de fácil mantenimiento. Las máquinas roladora de láminas son ampliamente usadas en la industria de construcción de embarcaciones, calderas, aviación, hidroeléctricas, químicos e industrias de manufactura de maquinaria.
Dada su amplia aplicación y uso, existen una gran variedad de roladoras, entre las que podemos encontrar como roladora, roladoras de láminas de acero, roladoras de alambre, roladoras en frío, entre otras.
Máquina roladora de láminas W11
Esta máquina roladora está compuesta de tres rodillos simétricos. El rodillo superior en simetría céntrica sobre dos rodillos inferiores. Éste rodillo superior, posee movimiento vertical hacia arriba y abajo. El reductor de velocidad ofrece cambios en los rodillos inferiores para ofrecer momento de torsión al espiral de la hoja de metal.
La presión de rolado es de 75 a 300 toneladas.
El espesor de placa es de 6mm a 25mm, y desde 1500mm a 3000mm de ancho.

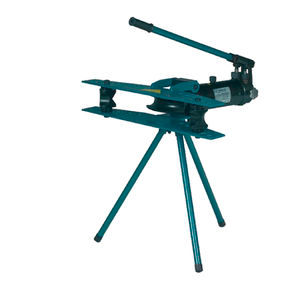


Cizalla Mecánica
La cizalla mecánica o el equipo de corte, adopta estructura de embrague en forma resistente con transmisión de engranajes abiertos.
También tiene piezas avanzadas como interruptor de pie y manual, opera con baja emisión de ruido y es muy conveniente de mantener.
Está fabricada con acero soldado en una estructura simple y compacta, con apariencia atractiva y bajo consumo de energía. Se usa ampliamente en el proceso de metales, plantas, motores, electrodomésticos, automóviles y muchas otras aplicaciones nacionales e internacionales.
Debido al calibre trasero que está ubicado en una longitud fija, la cizalla mecánica puede cortar a larga escala materiales para mejorar la eficiencia de una planta que trabaja con metales.
Esta máquina presenta estructura de acero, transmisión hidráulica y vibración para eliminar el estrés. Realiza el movimiento a través del cilindro que esta fijo en una de sus paredes, lo que puede simplificar el sistema hidráulico y hacerle más estable.
La máquina se esfuerza poco incrementando su vida útil y la de la cuchilla. Con su estructura estable se ajusta a la cantidad y a la fuerza de los golpes necesaria para el corte aumentando la productividad.
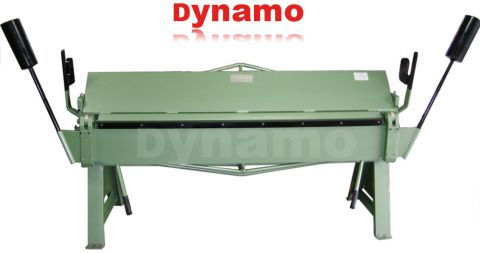
Dobladora de lámina
Las dobladoras son una herramienta ideal para hacer pliegues a las láminas de acero. La dobladora está construida en sólida placa de acero resistente al trabajo pesado, el cuerpo superior se puede ajustar para diferentes tipos de doblez y calibres de lámina. Además, estas máquinas son de fácil operación y requieren muy poco mantenimiento.
Dentro de sus principales ventajas, las dobladoras han sido fabricadas para enroscar láminas metálicas con precisión y producir cilindros rápidamente con mínimas partes planas en los extremos inicial y final. Esto facilita la soldadura posterior, la rigidez de la misma y la apariencia de las partes, entre otras cosas.
Propiedades:
1. La máquina dobladora de láminas emplea la estructura de acero de soldadura completa, por lo tanto poseen una gran fuerza y rigidez.
2. Tanques de aceite en los dos extremos de la máquina-herramienta se colocan en deslizadores, y pueden accionar directamente el trabajo de deslizamiento.
3. El eje torcido, el cual ha forzado a la utilización de tecnología de sincronización se ha utilizado en la estructura de sincronización de deslizadores.
4. La estructura de bloques mecánicos hace que el funcionamiento sea estable y fiable.
5. La ruta del control deslizante puede ajustarse rápidamente por el motor, y puede ser utilizado un ajuste manual fino. El contador puede mostrar todos los ajustes.
6. Estructura de compensación de la desviación bisel cuña se adopta para asegurar la obtención de una mayor precisión de plegado.